Digitalizing FISH
Background
The FISH project was an ambitious initiative aimed at revolutionizing the way warehouses operate by introducing a Smart Warehouse Inventory Management System tailored to the needs of FISH customers. As the Project Manager and UI/UX Designer for this project, I was responsible for overseeing its end-to-end development and ensuring the creation of an intuitive, efficient, and user-centric solution.
Overview
This system was designed to automate and streamline daily warehouse operations, offering a seamless workflow from inbound logistics to outbound distribution. Key functionalities included:
Receiving of Goods: Automating the recording and verification of inbound shipments, ensuring accuracy and reducing manual effort.
Internal Movement of Items: Enabling efficient tracking and relocation of goods within the warehouse to optimize storage and accessibility.
Raw Materials Processing: Facilitating the transformation of raw materials into finished goods on the production floor with precise inventory tracking.
Outbound to Customers: Streamlining the preparation and dispatching of goods, ensuring timely delivery and customer satisfaction.
The project’s core objective was to enhance operational efficiency, minimize errors, and provide real-time visibility into warehouse activities. By leveraging modern technologies and user-focused design principles, the FISH Smart Warehouse Inventory Management System empowered users to manage complex workflows with ease while optimizing productivity across all stages of the supply chain.
My role involved close collaboration with stakeholders, developers, and end-users to ensure the system met their unique requirements, delivering a solution that not only met but exceeded expectations.
The challenge
One of the key challenges during the FISH project was designing a system that could seamlessly integrate and automate diverse warehouse operations while accommodating the unique workflows and processes of FISH customers. Each stage—receiving goods, internal item movement, raw material processing, and outbound logistics—had distinct requirements and constraints that needed to be addressed within a unified platform.
Balancing these operational complexities with the need for an intuitive user experience posed a significant challenge. The system had to provide real-time inventory visibility and precise tracking while ensuring ease of use for warehouse staff with varying levels of technical expertise.
Additionally, managing stakeholder expectations and aligning design and development efforts to meet strict timelines added layers of complexity. It required thorough user research, iterative testing, and close collaboration across cross-functional teams to deliver a solution that was both functional and scalable for future needs.
My Role
UI/UX Designer
Project Manager
Duration
12 months
Client
Fish International Sourcing House Pte Ltd (FISH)
Tools
Figma, JIRA, google sheets, google meets
Design Process and Design Thinking
Our team, took on the double diamond design approach to tackle the re-design process. We aimed to incorporate the key phases of Discovery, Definition, Design and Delivery throughout the process. Whereby we went into Discovering user problems, Defining specific user problems, Designing potential solutions to these problems and lastly Delivering feasible and viable solutions.
Also under this double diamond process we took on the 5 key stages of design thinking. The 5 key phases of design thinking are, Empathize (learn about the audience for whom you are designing), Define (construct a point of view that is based on user needs and insights), Ideate (brainstorm and come up with creative solutions), Prototype (build a representation of one or more of your ideas to show to others), and Test (return to your original user group and testing your ideas for feedback).
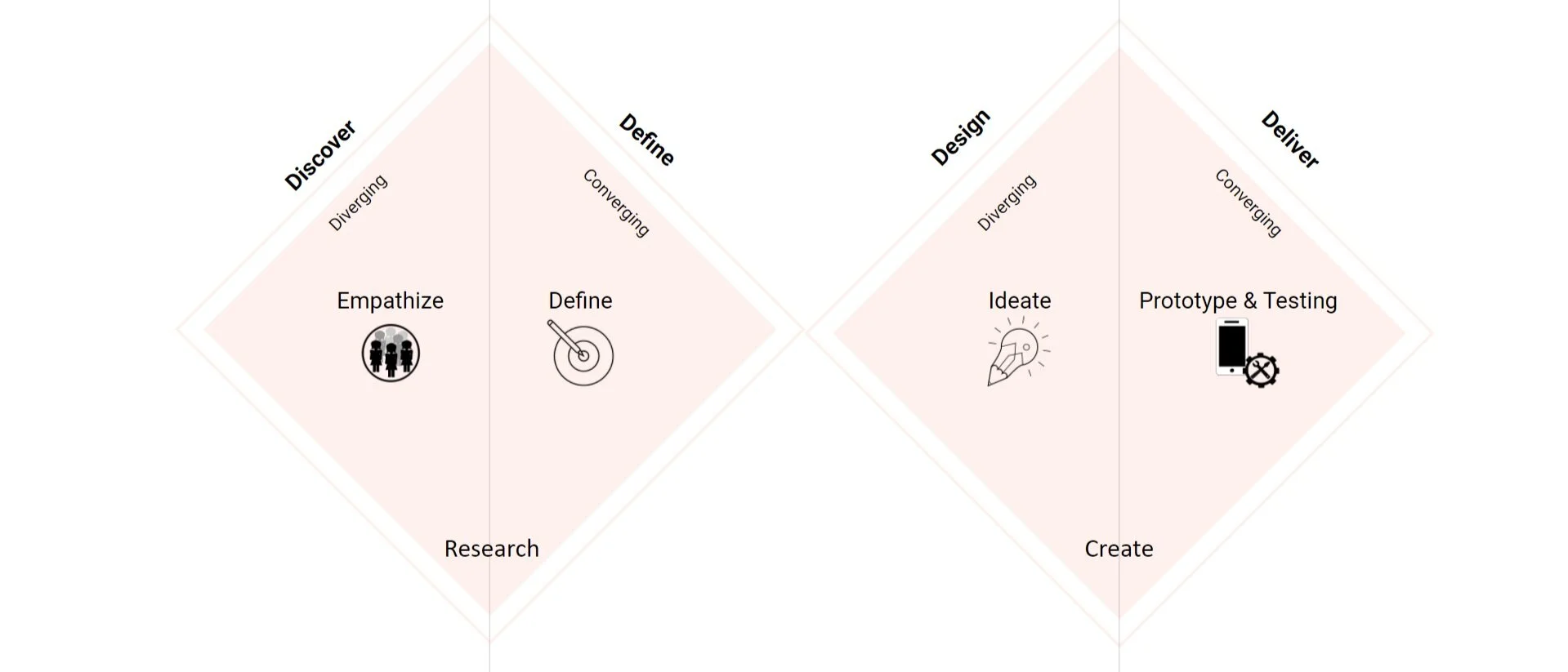
Discovery phase
User Requirement Gathering
Objective
The goal of the requirement-gathering phase was to understand the specific needs, pain points, and workflows of FISH customers to design a Smart Warehouse Inventory Management System that met their operational requirements and enhanced efficiency.
Approach
Stakeholder Interviews
Conducted in-depth interviews with warehouse managers, production staff, and logistics teams to understand their daily tasks, challenges, and expectations.
Gathered insights on current manual processes and identified areas for improvement through automation.
On-Site Observations
Observed day-to-day operations within the warehouse to map existing workflows such as receiving goods, moving items, raw material processing, and outbound logistics.
Identified inefficiencies, bottlenecks, and areas where technology could simplify operations.
Numerous In-Person and Online Meetings
Arranged several meetings with key stakeholders to prioritize features, align expectations, and gather feedback on initial concepts.
Used visual tools like user flows and process flows to facilitate discussions and validate assumptions.
Key insights
Pain Points:
Manual tracking of inventory was time-consuming and error-prone.
Lack of real-time visibility into stock levels and movements.
Complex workflows during raw material processing and outbound logistics.
User Needs:
An intuitive, user-friendly interface to reduce the learning curve for staff.
Automated workflows for inbound, internal, and outbound operations.
Real-time data visibility and reporting capabilities.
Feature Requirements:
Barcode and RFID scanning for tracking inventory movements.
Integration of raw material processing into inventory tracking using their weighing scales
Role-based access to ensure secure and efficient use of the system.
Dashboarding - for real-time visibility of current state of their raw process.
Competitive Analysis
To gain an understanding of what’s in the market right now, we conducted comparative and competitive research with 5 competitors (3 direct and 2 indirect competitors). Our goal was to compare and identify common features across these sites and potential opportunities for onePA to differentiate itself. More focus was on competitive analysis - particularly, the positives (what has been done well) and the negatives (what could be improved). The most important takeaway from this activity was learning how different websites organised their content and the overall layouts they used for those websites. These are the features that stood out and we considered adding to the current site.
Navigation Tree
We adopted the navigation tree way of displaying the menu from Zoho Inventory. This allows user for ease of use in navigating between modules and functions.
Recommendation section
Search filters and display table were adopted from Netsuite ERP. Provides better usability for users.
Define phase
Meet the personas
Warehouse Staff: "Emily Wong"
Age: 31
Role: Warehouse Operative
Background:
Emily has been working in warehouse operations for 5 years. Her role involves physical tasks such as receiving goods, relocating items, conducting stocktakes, and preparing shipments. Emily values tools that make her work more efficient and straightforward.
Goals:
Complete tasks accurately and efficiently with minimal disruptions.
Reduce manual effort in tracking and recording stock movements.
Ensure all items are correctly processed and labeled.
Pain Points:
Tedious manual data entry for stock updates.
Delays in locating inventory due to lack of real-time tracking.
Difficulty managing multiple tasks, such as picking, relocating, and inspections.
Behaviors:
Uses barcode and RFID scanners for inventory updates.
Regularly moves between warehouse zones, including receiving docks, storage racks, and packing areas.
Relies on straightforward, easy-to-use tools to complete tasks quickly.
How FISH Helps:
Simplifies item tracking with RFID and barcode scanning.
Streamlines task allocation with clear workflows and updates.
Provides mobile accessibility for quick stock updates and task management.
Warehouse Manager: "John Tan"
Age: 42
Role: Warehouse Manager
Background:
John has over 15 years of experience managing warehouse operations. He oversees inventory levels, team productivity, and order fulfillment. John is tech-savvy and open to adopting digital tools that streamline processes and reduce errors.
Goals:
Ensure smooth day-to-day warehouse operations.
Minimize inventory discrepancies and optimize stock levels.
Use data analytics to improve operational efficiency.
Collaborate effectively with stakeholders, including suppliers and logistics teams.
Pain Points:
Limited visibility into real-time inventory movement.
Difficulty tracking multiple processes, such as inbound, internal movement, and outbound logistics.
Time-consuming manual reporting and error-prone documentation.
Behaviors:
Regularly uses a tablet or laptop to monitor warehouse metrics.
Frequently communicates with warehouse staff and external stakeholders.
Relies on dashboards and real-time alerts to make informed decisions.
How FISH Helps:
Provides a centralized dashboard for real-time inventory visibility.
Automates reporting and stock movement tracking.
Offers intuitive tools for planning and optimizing workflows.
User Journey
User journey helped us to visualize user’s goals and the emotions they go through while completing certain tasks. It then helped us to narrow down the problem based on the users pain points.
Warehouse Staff (Emily Wong): User Journey Flow
Task Assignment
Receives a task notification on a mobile device to verify stock levels in a specific zone.
Execute Task (Receiving Goods)
Uses a barcode/RFID scanner to log incoming shipments.
Updates the inventory database directly through the mobile app.
Stock Movement
Moves items to the appropriate storage zones as instructed.
Logs item locations using the "Relocation" feature in the app.
Inspection and Updates
Conducts quality inspections for raw materials on the production floor.
Logs inspection details and updates item statuses (e.g., processed, defective).
Task Completion
Marks tasks as complete and syncs data with the central system.
Prepares for the next task, such as outbound processing or stocktaking.
Warehouse Manager (John Tan): User Journey Flow
Morning Routine (Analyze Dashboard)
Logs into the FISH system on a tablet.
Views real-time inventory metrics, alerts, and key performance indicators on the dashboard.
Identify Issues
Notices a stock discrepancy flagged in the system.
Checks the audit log to track the movement of the specific item.
Plan and Allocate Tasks
Assigns tasks to warehouse staff for stock verification and location adjustments.
Uses the task management module to prioritize urgent workflows.
Generate Reports
Exports a stock movement summary for the monthly review.
Shares the report with stakeholders via email directly from the platform.
Afternoon Routine (System Updates)
Reviews task completions and ensures operational stability.
Monitors real-time updates as tasks are completed by staff.
Problem Statement
Warehouse operations often face inefficiencies due to manual processes, lack of real-time inventory visibility, and difficulty in tracking item movements across various stages. This results in errors, delays, and increased workload for both management and staff. The challenge is to design a smart, user-friendly inventory management system that automates these processes, provides accurate tracking, and ensures seamless coordination between teams to enhance productivity and operational efficiency.
How Might We
streamline inventory tracking to provide real-time visibility and reduce manual errors?
How Might We
design an intuitive interface that simplifies complex warehouse workflows for users with varying technical skills?
How Might We
enhance coordination between warehouse staff and management to optimize task allocation and completion?
How Might We
integrate automation tools like RFID and barcode scanning to improve the efficiency of inventory management processes?
Solution Statement
Develop a smart, user-centric warehouse inventory management system that automates key operations such as receiving, tracking, processing, and outbound logistics. The system will leverage real-time inventory visibility, intuitive interfaces, and automation tools like RFID and barcode scanning to streamline workflows, reduce errors, and enhance coordination between staff and management, ultimately boosting overall efficiency and productivity.
Design Phase
Process flows
Process flows were created based on their persona to better understand the user needs.
This user flow illustrates the seamless integration between SAP and the Smart Warehouse Inventory Management System (SWIMS). It begins with SAP initiating data transfers for inventory updates, such as purchase orders or stock adjustments. SWIMS processes this data, updating warehouse operations like item receipt, relocation, or order fulfillment. The system then synchronizes completed tasks and stock movements back to SAP, ensuring real-time data consistency and enabling efficient decision-making across both platforms.
Click here for the full detailed process flow of the system.
Sketches
Based on the process flow, some basic sketches were drawn before diving into the wireframes.
Wireframes
Based on some sketch ideas, I then came up with the low fidelity wireframes.
Delivery Phase
Prototyping
The wireframes were then made into a prototype. Careful selection of color palettes and font types in alignment to their existing brand identity.

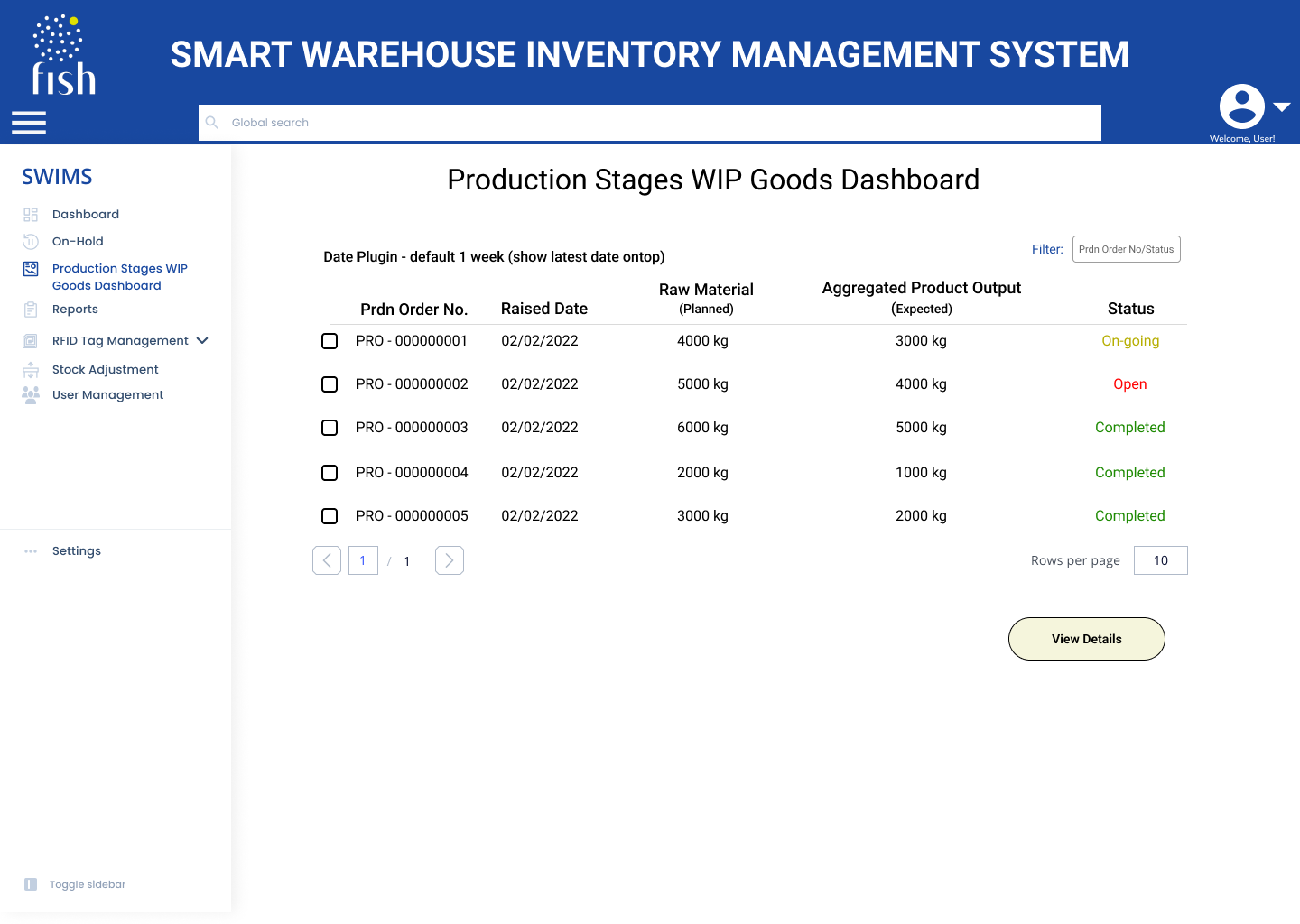
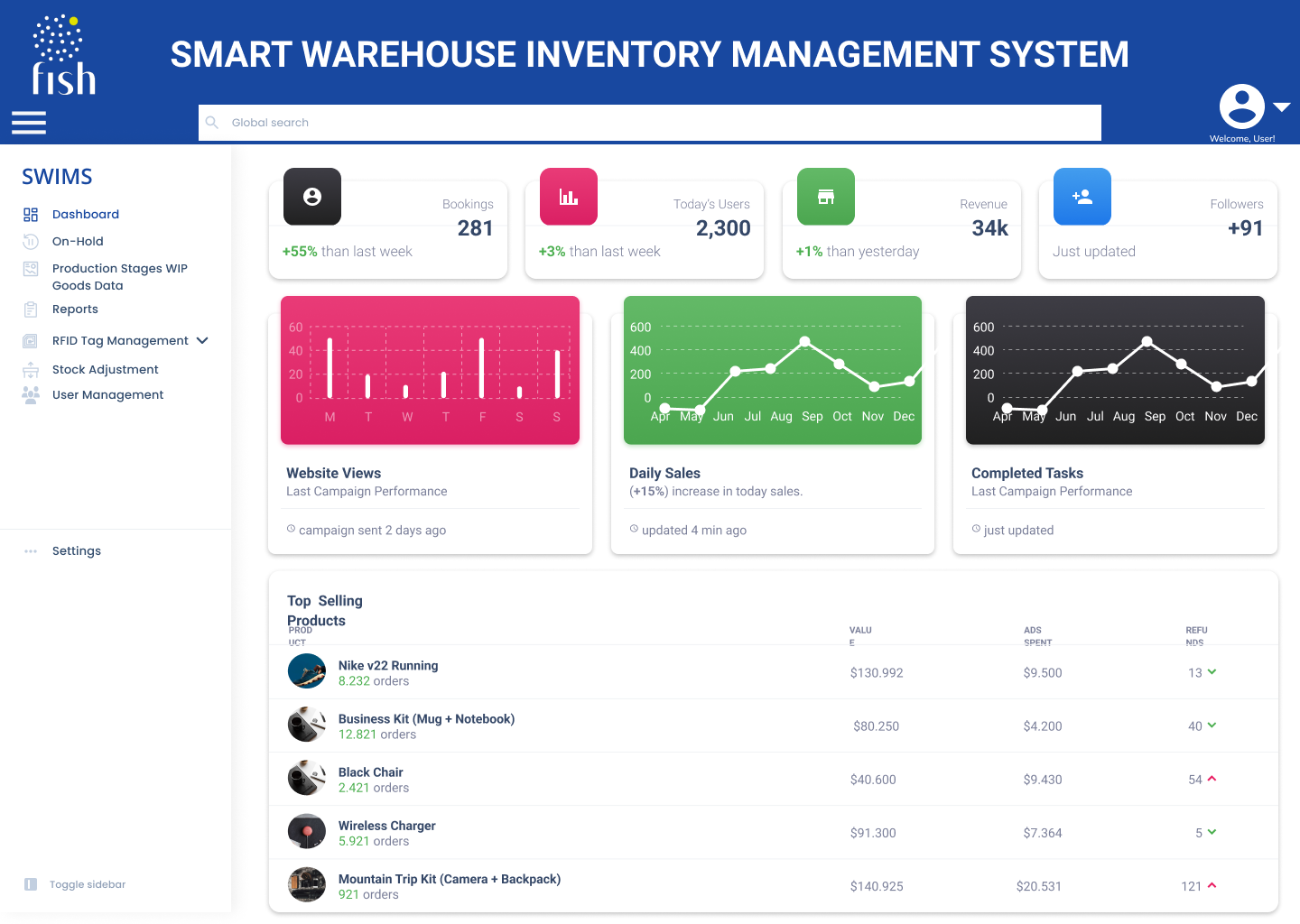
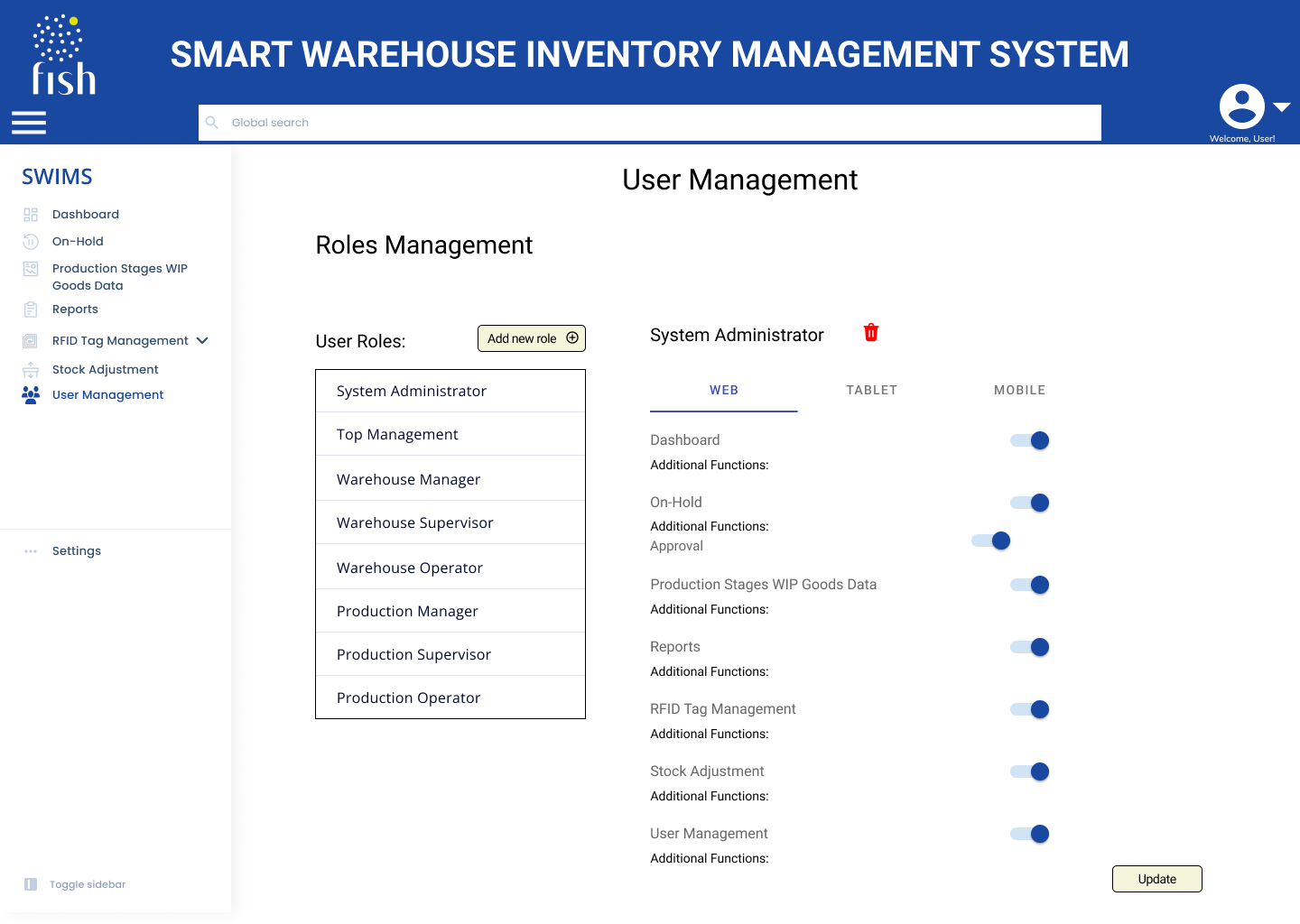
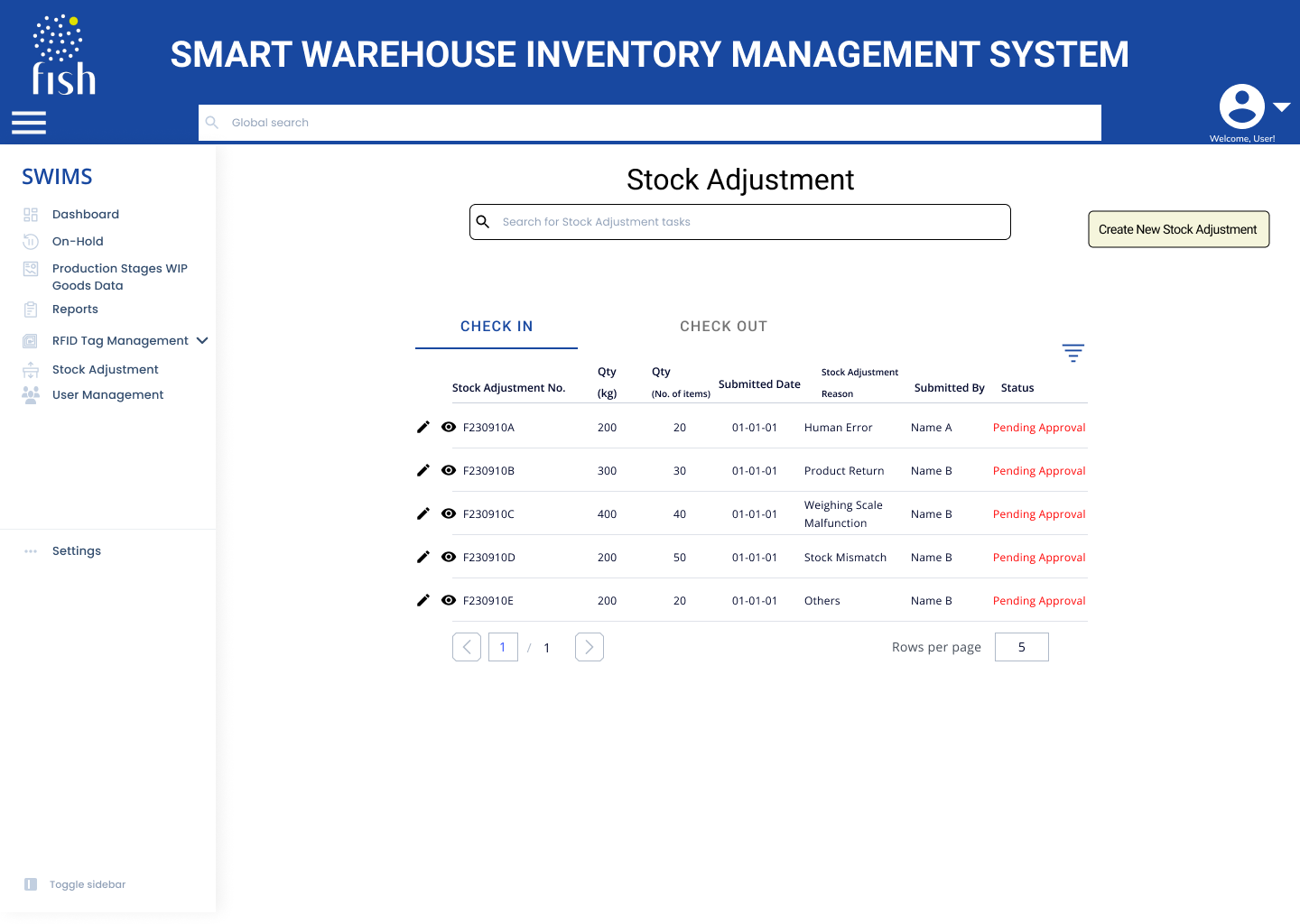
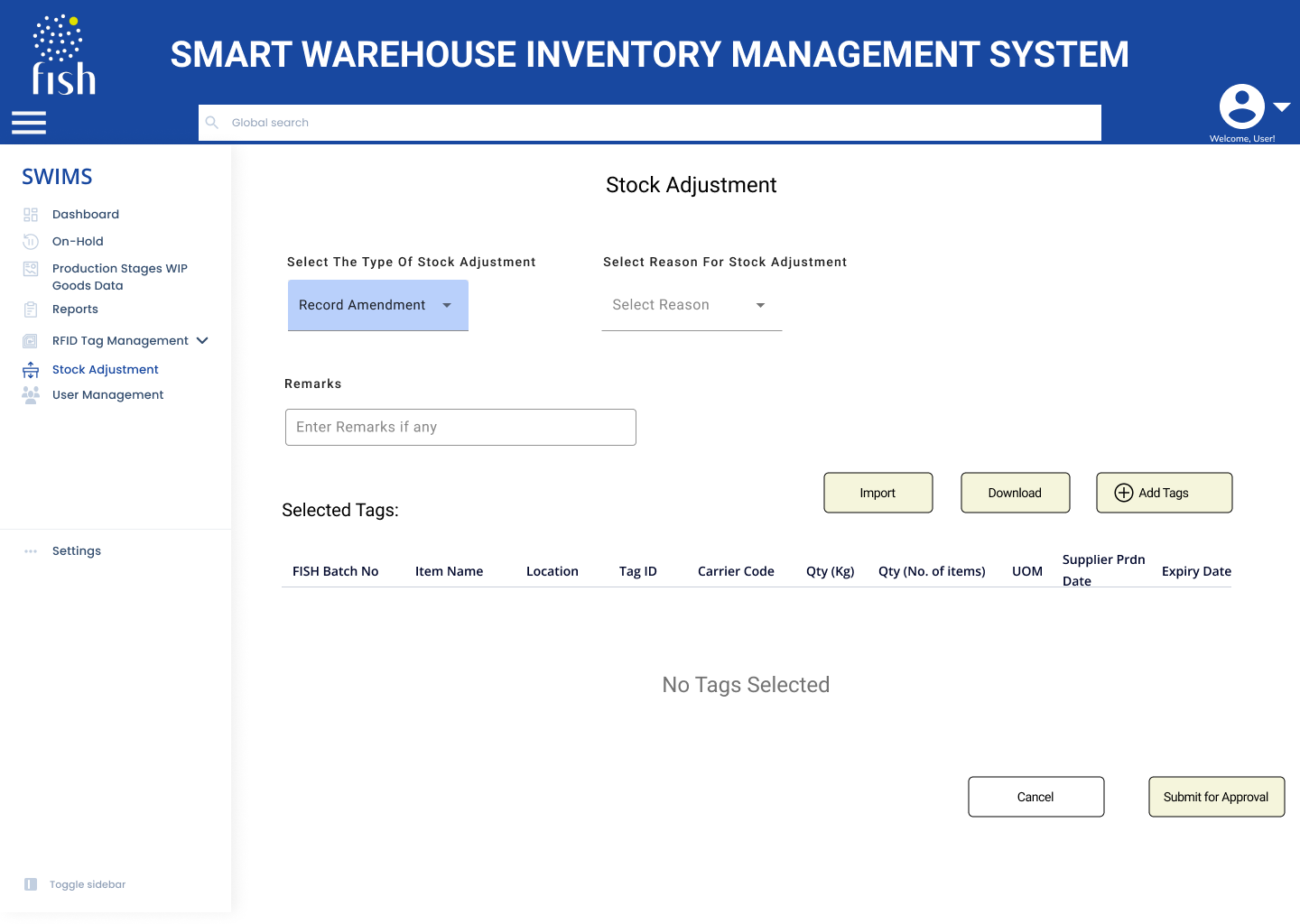
Prototyping
Prototype of FISH SWIMS Web and Mobile Application
User Acceptance Testing
User Acceptance Testing (UAT) was conducted to ensure the system aligns with business requirements and user expectations. Every test scenario and case was executed successfully, demonstrating that all functionalities work as intended. The seamless completion of UAT confirms the system's readiness for deployment.
Click here to view full UAT test script with result.
Next steps
Prepare for Go-Live:
Set a go-live date and perform pre-deployment checks to ensure all components are ready.
Plan and communicate the deployment timeline with all relevant stakeholders.
Monitor Post-Go-Live Performance:
Establish a support plan to monitor system performance and address any immediate issues post-deployment.
Collect user feedback to identify further improvement opportunities.
Plan for Future Enhancements:
Identify and prioritize additional features or improvements for subsequent releases based on UAT feedback and user needs.
Key takeaways
Importance of User-Centric Design:
Understanding user needs through research and feedback was critical in designing an intuitive and efficient system.
Collaboration is Key:
Close coordination between stakeholders, developers, and end-users ensured that the system met operational requirements and aligned with business goals.
Streamlining Complex Workflows:
Automating processes such as inventory tracking, item movement, and raw material processing significantly reduced manual errors and improved efficiency.
Scalability and Flexibility:
Designing the system to adapt to various operational needs, including RFID integration and customized workflows, future-proofs its functionality.
Thorough Testing Ensures Success:
Comprehensive UAT helped identify and resolve issues early, ensuring a seamless transition to go-live.
Effective Change Management:
Training and onboarding plans were essential to ensuring user confidence and smooth adoption of the new system.
Contact me.
Let’s create magic together!
ajmalishak@gmail.com
(+65) 8180 7547
109 Whampoa Road
Singapore - 321109